Asphalt Batch Mix Plant
AGGREGATES DRYER WITH BURNER:
The dryer drum, with a series of flights inside, which have the function of lifting the virgin material and heating it through contact with the hot gas produced by a modulating type burner with maximum fuel combustion efficiency. A burner is mounted at the discharge end of the drum for higher heating efficiency by counter flow heating.
The heat of the flame inside the dryer is conveyed to the aggregates via thermal radiation, by conduction &convection due to close thorough contact of aggregates with hot gases produced by burning of fuel.
It is natural that combustion exhaust gases, fine dust and water vapor are produced inside the dryer, and these are then passed through a bag filter via primary dust collectors before being released into the atmosphere.
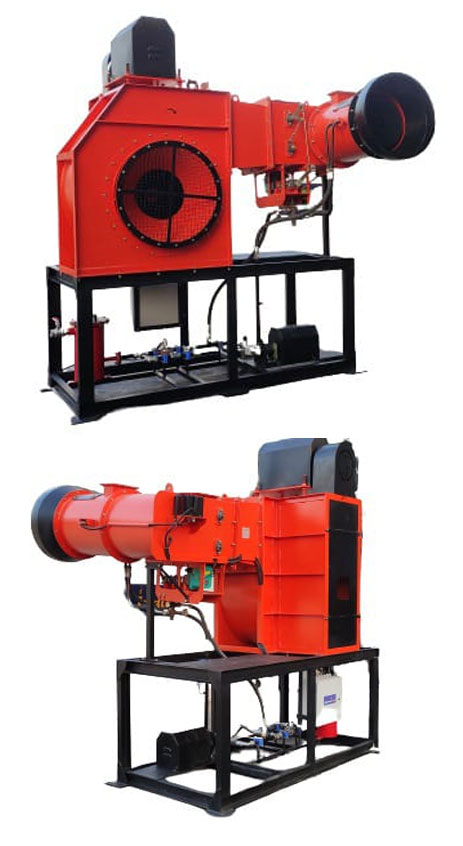
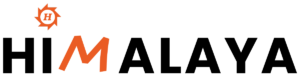
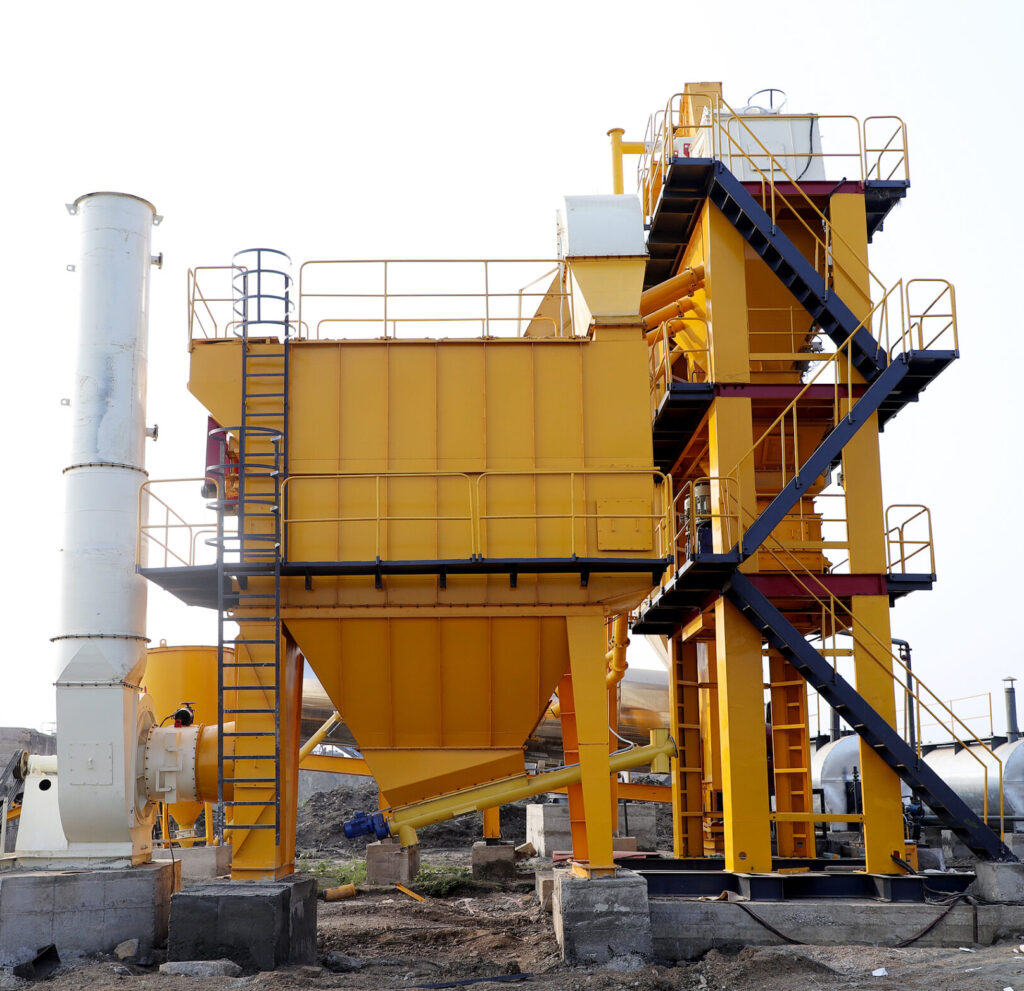
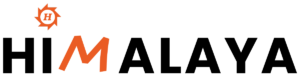
THE BAG FILTER:
Due to increasingly restrictive limits 150mg/Nm' for atmos- pheric emissions, together with new technologies for greater filter efficiency, problems related to environmental impact have now been greatly simplified.
Filler materials collected in the bottom hopper of RA type bag-filter with a number of fabric filter bags, then conveyed by a screw conveyor and bucket elevator into a surge hopper, ready to be weighed and re-fed into the mixer in the correct quantity.
The filler plays a fundamental role in regulating the asphalt adhesion and improving the bitumen binding to the aggregates. So, bag filter with proper filtering efficiency play major role in asphalt batch plant.
Batch Tower
Fully enclosed inclined linear vibrating screen with high quality vibrating screen cloths, contribute to top notch performance. The inclined linear vibrating screen is provided with duplex spring absorbers, and is powered with two numbers of six-pole maintenance free vibro motors. The free-floating design prevents any vibration from being transferred to the weighing scales. A wider platform with easy access eases the maintenance of the screen.
Highly reliable weighing system load cells and an easy calibration system makes the HBM series highly popular with site engineers and plant operators.
The 3D mixer unit is the heart of the HBM plants and has a large live zone, realizing a quick and even mixing of asphalt. The mixer unit is hot oil jacketed and supplied with a low- maintenance oil-bath type chain drive. The paddles, arms and tips are made of wear resistant high nickel hardened cast alloy steel. The reversible design of the paddle tips ensures a lower operating cost.
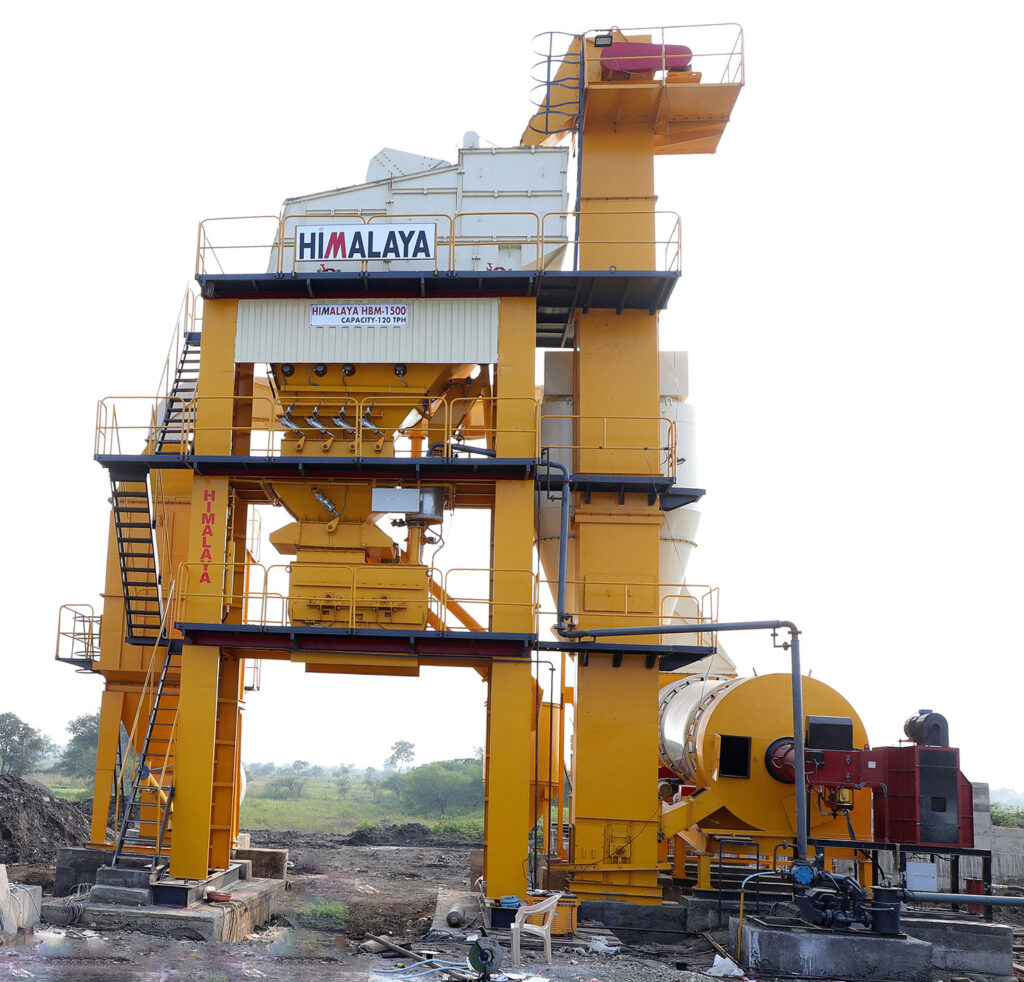
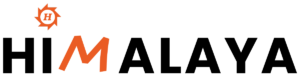
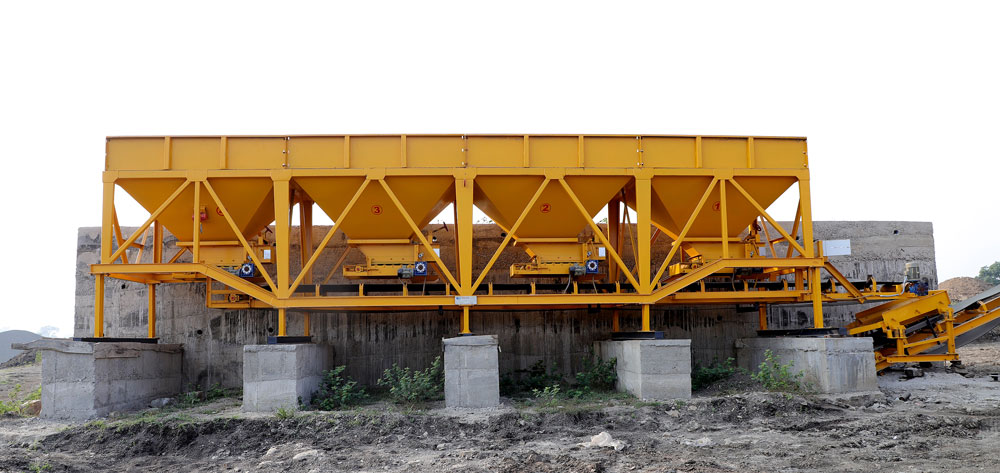
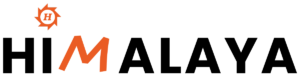
Cold Aggregate Bin Feeders
18 Years of experience in this industry units means design expertise or top performance even under the toughest of operating conditions. The Bins are all-welded and modular in construction, permitting easy addition of bins to meet growing needs. Steep bin walls and valley angles allow free flow of aggregates from the feeders minimizing hold-up of materials in the corners and bridging with sticky aggregates. The bins suppled with adjustable calibrated gate openings and variable speed feeder drives together offer a total proportional control, greater flexibility and accuracy of operations.
Control System
Fully computerized air-conditioned control cabin with onboard electrical power control console, distribution switch board, fully automatic process and sequence control are a standard on all HBM series plants.
User-friendly software on the computer with a parallel PLC main machine interface gives you total reliability and ensures top notch performance.
- Automatic free fall compensation
- Fail proof power interlocks and process controls
- Automatic cold aggregate feeder controls linked with mix
- design and hot bin levels
The control is equipped with function keys and numeric keys, and does not require skills for operation.
The operator can monitor the complete process control, motor status and pneumatic controls through the color CRT display.
SCADA features:
- Docket printing and inventory management
- Provisions to print, store and email production details, mix properties, etc.
- Online fault detection with remote connectivity and solution
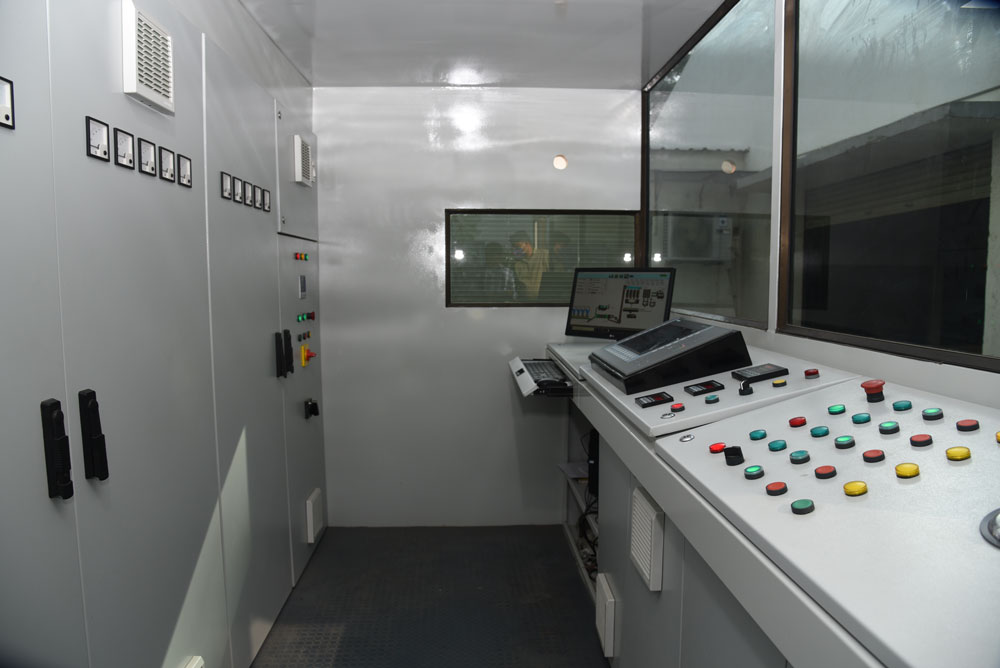
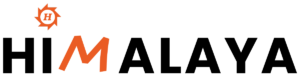
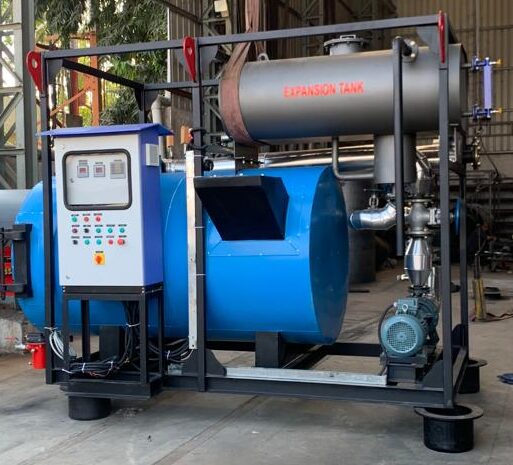
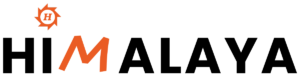
THERMIC OIL HEATER
The HBM series plants are supplied with hot oil jacketing on bitumen pipe line, asphalt pumps, bitumen weigh hopper section and Pug mill body; Opting for hot oil heating reduces asphalt pump binding, asphalt pipe line blocking, smoother bitumen weigh batcher and pug mill
operations.
The Thermic oil heater is supplied with independent automatic control panel including oil temperature indicator controller, low level switch, low circulation pressure switch over temperature cut of thermostat burner operating circuits. Capacity range up to 500 000 kcal/hr
FEELER FEEDING AND STORAGE SOLLUTION
Himalaya offers a wide range (4-40 Tons) of foreign filler storage solutions. The filler from the silo is transported into the filler elevator on the batching tower, which then is weighed and mixed in the pug mill unit.
The filler silos can optionally be supplied with filler feeding bucket elevator to suit bagged filler feeding. As a option the filler silos are supplied with level indicators and process interlocks.
BETUMEN HEATING AND STORAGE SOLLUTION
The indirect heating tanks are supplied with a high efficient thermic oil heater. All tanks are supplied with auto thermostatic controls and level indicators.
HOT MIX STORAGE SILO
Himalaya offers a complete range of Hot mix storage solution 25 t to 80 t, to meet plant requirements. Hot mix storage silos can be offered with options to store different types of mix designs to meet varied site demands.
All HBM series are supplied with state of the art fully automatic controls together with automated safety and un-interrupted productivity. By opting for a hot mix silo customers gain large benefits. achieve increase efficiencies through longer continuous production runs. Fuel savings - thanks to the uninterrupted and constant dryer drum burner operations. Helps cater to clients with different mix design requirements. Reduce the number of transporting trucks.
Technical Specification
Main plant
HBM 1000 | HBM 1200 | HBM 1500 | HBM 2000 | HBM | ||
Plant capacity @ 3% | moisture content | 80 tph | 100 tph | 128 tph | 160 tph | 2500 200 tph |
Cold Feed Bins | No. of Feeders*/Total Cap | 4/25m3 | 4/31.25m3 | 4/37.5 m³ | 4/43.75m3 | 5/46.50m2 |
Charging Conveyor | Capacity | 100 tph | 120 tph | 140 tph | 180 tph | 220 tph |
Dryer Drum | Diameter X Lenth | 1.8mx7n | 1.8mx7m | 2.1mx8m | 2.1 m x 8 m | 2.3mx9m |
Drive Type | Saddle type chain drive | Four wheeled Friction | drive | |||
Burner | Capacity | 6.5MW | 9 MW | 11.8 MW | 13.6 MW | 17.3 MW |
Type | High pressure, | Fully automatic, | modulating | |||
Fuel* | Diesel | Diesel | Diesel | Diesel | Diesel | |
Pilution Control Unit | Dual Stage Type | |||||
Primary | Centrifugal Double Cyclone | 1.4mx3m | 1.4 m x 3 n | 1.4mx3m | 1.4 m x 3 m | 1.4 m x 3 m |
Secondary | Wet Dust | Type / Bag House | Filter | |||
Bag House Filter | Reverse air flow | type with emission | level 150 mg/Nm³ | |||
Filtering Area | 285 m² | 325 m² | 390m2 | 435 m² | 590 m² | |
Hot elevator | Capacity | 100 tph | 120 tph | 140 tph | 180 tph | 220 tph |
Screening Unit | Type | Four deck vibrating | ||||
Capacity | 100 tph | 120 tph | 140 tph | 180 tph | 220 tph | |
Hot Aggregates Bin | Number of Bins | 4 | 4 | 4 | 4 | 4 |
Aggregates Weigh Bin | Capacity | 1000 kgs | 1250 kgs | 1500 kgs | 2000 kgs | 2500 kgs |
Filler Weigh Bin | Capacity | 200 kgs | 200 kgs | 300 kgs | 300 kgs | 400 kgs |
Bitumen Weigh Bin | Capacity | 150 kgs | 150 kgs | 225 kgs | 225 kgs | 300 kgs |
Filler Feeding System | Filler Elevator Capacity | 14 tph | 14 tph | 21 tph | 21 tph | 21 tph |
Filler storage Bin Capacity | 0.4 m³ | 0.4 m³ | 0.6m3 | 0.6m3 | 0.6m3 | |
Asphalt Feeding Pump | Capacity | 240 lpm | 240 lpm | 450 lpm | 450 lpm | 450 lpm |
Asphalt Spray Pump | Capacity | 460lpm | 460 lpm | 800 lpm | 1000 lpm | 1000 lpm |
Mixing Unit | Type | Twin shaft | hot oil jacketed | pugmill unit | ||
Capacity | 1000 kg/batch* | 1250 kg/ batch* | 1600 kg / batch* | 2000 kg / batch* | 2500 kg/batch* | |
Cycle Time | 45 Secs. | 45 Secs. | 45 Secs. | 45 Secs. | 45 Secs. | |
Control Panel | Type | Fully | computerized with manual | over-ride |
Accessories
Filler Silo | Capacity | 10 / 15 / 25 / 40 tons |
Bitumen Tanks | Capacity | 15 / 25 / 30 / 50 tons |
Heating Type | Direct / Hot Oil heating type | |
Hot Oil Heater | Type | Normal Pressure horizontal tubular boiler with oil fired burner |
Capacity | 3/4/5 Lac Kcal / hr. | |
Hot Mix Storage Silo | Capacity | 25 / 50/25×2/ 80 tons |